

How does CNC Metal Bending Work?
CNC Metal Bending: A new Standard of Precision.
Apr 4, 2024
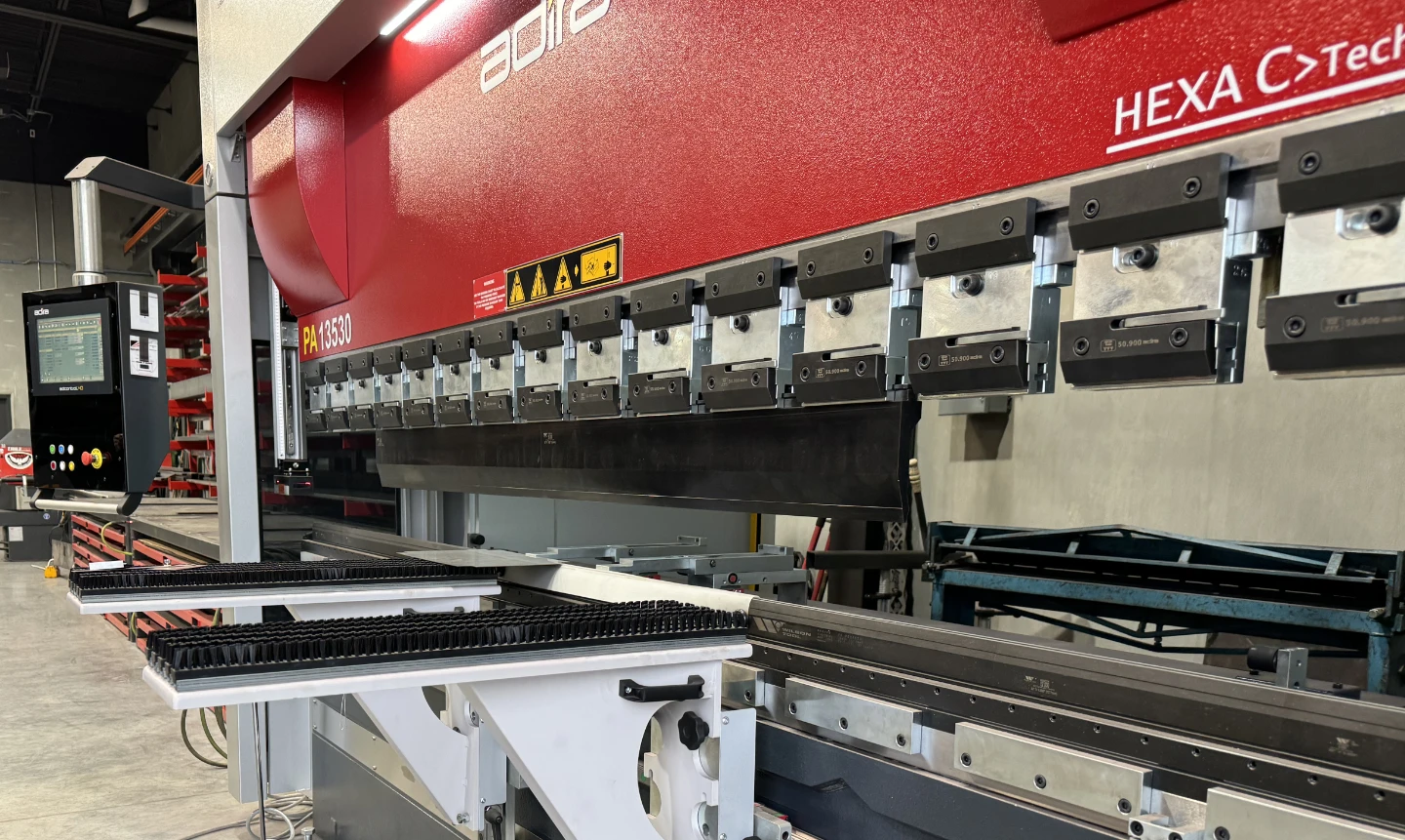
CNC metal bending is a sophisticated fabrication process that manipulates metal into precise shapes and angles using computer-controlled machines. This process is integral to manufacturing a wide range of metal products, from small brackets to large architectural components. Here’s an overview of how CNC metal bending works:
1. Design and Programming
Initial Design: The process begins with a detailed design, typically created in a CAD (Computer-Aided Design) program. This design specifies the dimensions, angles, and specific features required for the finished product.
Programming: The design is then converted into a set of instructions for the CNC bending machine. This programming phase involves specifying the bending sequence, angles, and force required for each bend. The software calculates the most efficient bending sequence and makes adjustments for material properties, ensuring precision in the final product.
2. Material Selection and Preparation
Before bending, the correct type and thickness of metal are selected based on the requirements of the project. Materials commonly used in CNC bending include steel, aluminum, and stainless steel.
The metal sheet or plate is then prepared, which may involve cutting it to size and marking bending lines as guides.
3. Bending Process
Machine Setup: The CNC bending machine, often a press brake, is set up with the appropriate tools and dies based on the thickness and type of metal, as well as the required bend angles.
Positioning: The metal is placed on the machine's bed, positioned against backgauges to ensure it's aligned correctly for the bend.
Bending: Once the metal is in place, the machine’s upper beam, equipped with a punch, descends and presses the metal into the die, creating the bend. The force and depth of the bend are precisely controlled by the machine, following the pre-programmed instructions.
4. Quality Control and Finishing
After bending, each piece is inspected for accuracy, ensuring it matches the design specifications. Any necessary adjustments are made at this stage.
Additional finishing processes, such as deburring, polishing, or coating, can be applied to improve the appearance and resistance of the metal to corrosion.
Advantages of CNC Metal Bending
Precision and Consistency: CNC metal bending provides high levels of precision and repeatability, crucial for large production runs where every piece must be identical.
Efficiency: The process is highly automated, reducing the time and labor costs associated with manual bending methods.
Flexibility: CNC bending machines can quickly switch between different jobs and handle a variety of metal types and thicknesses, making them versatile tools in metal fabrication.
Minimized Waste: Precision bending reduces material waste, as the process ensures that each bend is made accurately, avoiding the need for rework or excessive finishing.
CNC metal bending has revolutionized the metal fabrication industry, enabling the production of complex, high-quality components with speed and efficiency. Its integration into manufacturing processes underscores the ongoing shift towards automation and precision in the fabrication sector.